Grease fitting and heim joint shift linkage!!!
#1

Added the grease fitting mod to the forward section of my engine case the shift rod goes through, and added the stainless shift linkage with heim joints.
Man it sure makes for some sweet shifting now. Really like night an day...
If you have not done so I highly recommend it. Will put a picture up soon.
Man it sure makes for some sweet shifting now. Really like night an day...
If you have not done so I highly recommend it. Will put a picture up soon.
#4

If you look at the picture below, you can see a grease fitting in the casing for the shift link rod.
It means that you have to dis-assemble the linkage on the engine side to allow the shaft to be pulled out, then get a grease fitting and tap. Drill the pilot hole then the tap size hole and then I put the tap into the drill on low speed and drilled the tap into the hole in the case. Put the air hose upto it to blow of any shavings and ran a small screw driver into the shaft side (not the fresh taped hole) to see if any other burs would be inside. Hit it with air again, then assembled with my new grease fitting (which I added a bit of locktight), when all assembled, just added a quality marine grade water resistant lithium grease (Castrol grease is what I always keep in my gun).
And now the shift linkage is tight and smooth as silk.
[IMG]local://upfiles/4133/963D2461522F49FABAA8C0F28C0C8FC3.jpg[/IMG]
It means that you have to dis-assemble the linkage on the engine side to allow the shaft to be pulled out, then get a grease fitting and tap. Drill the pilot hole then the tap size hole and then I put the tap into the drill on low speed and drilled the tap into the hole in the case. Put the air hose upto it to blow of any shavings and ran a small screw driver into the shaft side (not the fresh taped hole) to see if any other burs would be inside. Hit it with air again, then assembled with my new grease fitting (which I added a bit of locktight), when all assembled, just added a quality marine grade water resistant lithium grease (Castrol grease is what I always keep in my gun).
And now the shift linkage is tight and smooth as silk.
[IMG]local://upfiles/4133/963D2461522F49FABAA8C0F28C0C8FC3.jpg[/IMG]
#5
#6

ORIGINAL: dawg
Buy a 45 degree zerk and replace the steering neck zerk with the 45 and put the OE one in the shifter
ORIGINAL: Boxs
Ram- can you explain a little more about this mod, it sounds
like I may want to do this.
TIA- Boxs
Ram- can you explain a little more about this mod, it sounds
like I may want to do this.
TIA- Boxs

Thanks,
Gary
#7

ORIGINAL: Ram
I'm just looking for those little plastic deals to put on it to keep the dirt out of the zerkshole with the check ball and spring!
Thanks,
Gary
I'm just looking for those little plastic deals to put on it to keep the dirt out of the zerkshole with the check ball and spring!
Thanks,
Gary

Trending Topics
#8

ORIGINAL: dawg
http://www.fittingsandadapters.com/zerkcap.html If ya can afford the whopping $.11
ORIGINAL: Ram
I'm just looking for those little plastic deals to put on it to keep the dirt out of the zerkshole with the check ball and spring!
Thanks,
Gary
I'm just looking for those little plastic deals to put on it to keep the dirt out of the zerkshole with the check ball and spring!
Thanks,
Gary

Thanks,
Gary
#9

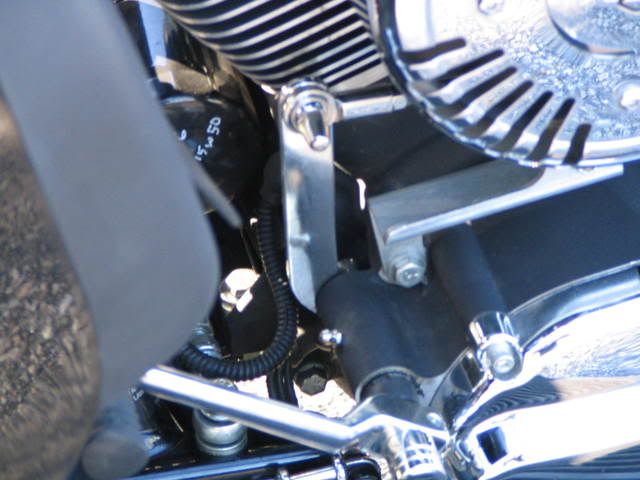
Some additional info on how to do this:
I've taken the entire assy apart and removed the rod accross the front of the casing. A set of brass bushings reside inside the casing, one left and one on the right of the thing.
The inside also needed to be cleaned out of filings from drilling and tapping. So having it appart not only provided clear path, and to see if any bur's were needing to be scraped. Not to mention I didn't want to dimple or drill into the rod with it still in the case.
I've assembled all my materials, bit, tap, zerk, and heim joint rod assy prior to disassembly. All to save time as well.
Drill bit, was a Vermont American #3, partnumber 11803. Size = .2130 inch which is 5.41mm. Standard wire gauge (steel twist) drill bit. Not coblt or titanium tip or anything fancy its just going though barley 1/4" of aluminum. This is the right size for the tap, used Hi-speed on the drill.
Tap is also a Vermont American #3, partnumber 20069. Size 1/4-28 NF. Also centered this in my drill used taping paste on the tap and let her rip at slow speed and only went in to the hole just enough to bring tap end 1/3 of way into hole. Then cycled in and out a couple times to chase the threads.
Cleaned with compressed air, and inspected for hanging bur's inside.
Put hi-temp lock tight red onto Stainless Steel zerk fitting, size 1/4-28 and snugged up. Not put a lot of torque onto it. I wanted threads to be tight but not stripped, lock tight does the rest.
They were fairly snug in not running tap all the way to the hilt in and out a bunch of times making it a sloppy fit.
From that point its just a reassembly process. Got that all finished and lock tighted those Heim joint nuts as well.
Then hit with grease.. I use Castrol Marine Grade Lithium. All that I've used for years for everything from wheel bearings to ball joints and tie rod ends.
Sorry to not include into the thread from the start.
Good luck with it, you will be amazed how firm it feels and postive it shifts from now on after you do this mod.
Last edited by Ram; 08-13-2008 at 07:02 PM. Reason: Add photo!
#10

Nice mod. I'll have to remember this the next time I take mine apart.
While in there a chrome spacer to replace the black one and a wave washer works well.
http://www.cvoharley.com/smf/index.php?topic=21256.0
While in there a chrome spacer to replace the black one and a wave washer works well.
http://www.cvoharley.com/smf/index.php?topic=21256.0
Thread
Thread Starter
Forum
Replies
Last Post