Whats better for wiring handlebars?
#21

If you can cut and solder wire, just do it yourself. Those wire extensions are nice, but expensive for what you get. If you are not confident splicing wires, buy the extensions.
Just make them long enough to hide the connectors back in the frame. 16 or 18 AWG wire will work just fine. 14 is too heavy.
Just make them long enough to hide the connectors back in the frame. 16 or 18 AWG wire will work just fine. 14 is too heavy.
#22

But did want to say that I have personally shrink tubed wire spliced together for an underwater pond pump. The pump was still running over a year later.
If you get the right size shrink tube and use a enough heat these things are tight.
But admittedly the pump wire was sheathed in round SO cable which would seal better than just several wires group openly together. But even then I think one could spread some silicone over the wires before sliding the heat shrink into place.
A $9 heat gun will do a much neater job than a propane torch. It slowly pulls it all up neat with no black scorch scars.
The following users liked this post:
Uncle Mok (10-22-2023)
#23

Don't mean to knock terminal connectors, since all of mine hold fine.
But did want to say that I have personally shrink tubed wire spliced together for an underwater pond pump. The pump was still running over a year later.
If you get the right size shrink tube and use a enough heat these things are tight.
But admittedly the pump wire was sheathed in round SO cable which would seal better than just several wires group openly together. But even then I think one could spread some silicone over the wires before sliding the heat shrink into place.
A $9 heat gun will do a much neater job than a propane torch. It slowly pulls it all up neat with no black scorch scars.
But did want to say that I have personally shrink tubed wire spliced together for an underwater pond pump. The pump was still running over a year later.
If you get the right size shrink tube and use a enough heat these things are tight.
But admittedly the pump wire was sheathed in round SO cable which would seal better than just several wires group openly together. But even then I think one could spread some silicone over the wires before sliding the heat shrink into place.
A $9 heat gun will do a much neater job than a propane torch. It slowly pulls it all up neat with no black scorch scars.
#24

Something else to consider is that when you cut the wires, cut them each in slightly different locations (meaning: stagger the locations). That way when you splice them back together you don't end up with a big "clump" of wire connectors in the same location. It helps to make it easier when you pull the wires...
Yep. All you do is just give yourself all the time you need (don't rush it), either draw the connectors on a sheet with which wire goes where (or a picture), and it's a piece of cake.
I also acquired some braided nylon wire loom (as well as some stainless braid) to cover the wires coming out of the bars and down to the backbone. I wasn't sure if I wanted the stainless (to match my cables/brake lines) or not. Turns out the black nylon braid looked better.
I also acquired some braided nylon wire loom (as well as some stainless braid) to cover the wires coming out of the bars and down to the backbone. I wasn't sure if I wanted the stainless (to match my cables/brake lines) or not. Turns out the black nylon braid looked better.
I'm bettin those plug assy's were not redone correctly which allowed them to come apart and short out.
Everytime you make a connection you create a chance for failure. There is less a chance if you use plug assy's and they are put together correctly. Everytime you use solder you put more resistance in the wire run. Maybe its negligible maybe not. But its there. I have also seen solder joints gather moisture over time. No shrink tube is going to keep 100% of the moisture out. Doing it more than once helps, but in all my years of building cars and working on bikes I have found sticking to conventional terminal block assy's to be much more reliable, and breaking down on the road with shorted wires in your bars is a whole lot more of a b!tch than when in a car, so I go with what I have found to work the best for me. My bud also agrees and he's been a HD wrench, service mgr and bike builder for nearly as long. So its not just me.
So I guess we'll just have to agree to disagree. I sure cannot question your work or creations JRK, you make some wicked cool bikes.
Everytime you make a connection you create a chance for failure. There is less a chance if you use plug assy's and they are put together correctly. Everytime you use solder you put more resistance in the wire run. Maybe its negligible maybe not. But its there. I have also seen solder joints gather moisture over time. No shrink tube is going to keep 100% of the moisture out. Doing it more than once helps, but in all my years of building cars and working on bikes I have found sticking to conventional terminal block assy's to be much more reliable, and breaking down on the road with shorted wires in your bars is a whole lot more of a b!tch than when in a car, so I go with what I have found to work the best for me. My bud also agrees and he's been a HD wrench, service mgr and bike builder for nearly as long. So its not just me.
So I guess we'll just have to agree to disagree. I sure cannot question your work or creations JRK, you make some wicked cool bikes.
I believe a solder joint would be a better connection then any terminal block/ connector, nothing to come loose or corrode. Also gives a full contact connection as opposed to a partial connection that is typical in a connector. Solder two wires together then pull them apart until it breaks, "more often" than not, the wire will break and the solder joint will be intact, try that with a connector and you'll get undesirable results.
If your worried about moisture, just use the appropriate size shrink tubing so that it shrinks down tight enough around the wires insulation, and/or add a bit of silicone sealant to the solder joint before you slide the shrink tubing over it.
As far as your bud being a HD wrench, am I suppose to assume that he a good mechanic and his opinion should over ride my opinions?

To the original poster, another thing to do is make sure you deburr any sharp edges within your handlebars, and while your in there you might want to clean up the rest of the wiring: https://www.hdforums.com/forum/showt...eferrerid=9012

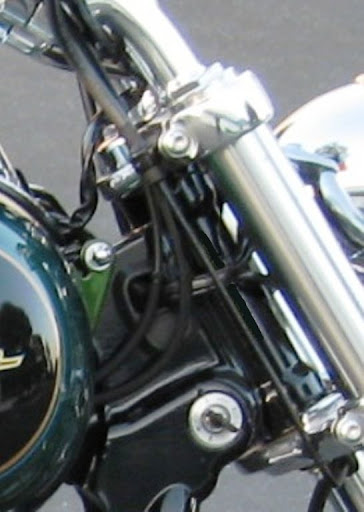
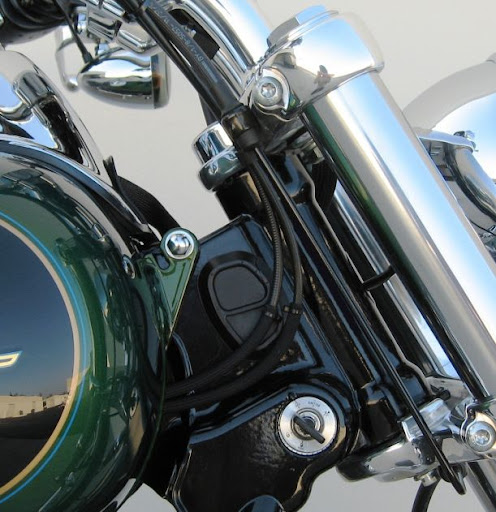


#26

When you solder you are splicing similar material, you are not using the solder to connect the wires, but to secure them permanently. The wires should be twisted together first.
As a Journeyman electrician for over 20 years, I have made a few electrical connections, originally wiring was always soldered and it lasted for years, longer than a lot of connector type connections we now do.
There is still **** and Tube wiring out there that is just fine as long as it has not been tampered with, **** and Tube was soldered.
#27

RE:glideridemike
[but if you're out away from any power source, a torch works. LOL Y'all do whatcha gotta do, and good luck with it!]
Yep you're right on that one, used a butane cigarette light once.
RE: 8541hog
[There is still **** and Tube wiring out there that is just fine as long as it has not been tampered with, **** and Tube was soldered.]
Yep all true, but boy that **** and tube was some crude installation. Years ago I worked with a crew that replaced all that when the client bought an old historic home. Course I guess it was top of the line in it's day. And LOL "not tampered with" would include not stepping on it in the attic and breaking the insulators etc.
[but if you're out away from any power source, a torch works. LOL Y'all do whatcha gotta do, and good luck with it!]
Yep you're right on that one, used a butane cigarette light once.
RE: 8541hog
[There is still **** and Tube wiring out there that is just fine as long as it has not been tampered with, **** and Tube was soldered.]
Yep all true, but boy that **** and tube was some crude installation. Years ago I worked with a crew that replaced all that when the client bought an old historic home. Course I guess it was top of the line in it's day. And LOL "not tampered with" would include not stepping on it in the attic and breaking the insulators etc.
Last edited by R_W_B; 12-16-2010 at 01:46 PM.
#28

I've done DIY internal extentions for apehangers (read: cut the wires in the middle and splice about 20 inches of new wire in between). And then I redid them after shorting problems. I think I found the 8 cond wire I used at a farm supply store. I'm all for old school, but if you can do plug-and-play in this case, that sounds like a good deal.
Thread
Thread Starter
Forum
Replies
Last Post